Path Planning for Industrial Robots Working Collaboratively on a Task
This research was done as part of my Master’s thesis. You can find the full thesis (in downloadable format) here: https://etd.ohiolink.edu/acprod/odb_etd/etd/r/1501/10?clear=10&p10_accession_num=dayton1701617256204635
Objective:
To develop offline-coordination planning techniques for multi-robot systems with partially shared workspaces that enables them to allocate and perform manufacturing tasks in a time-effective and computationally efficient manner.
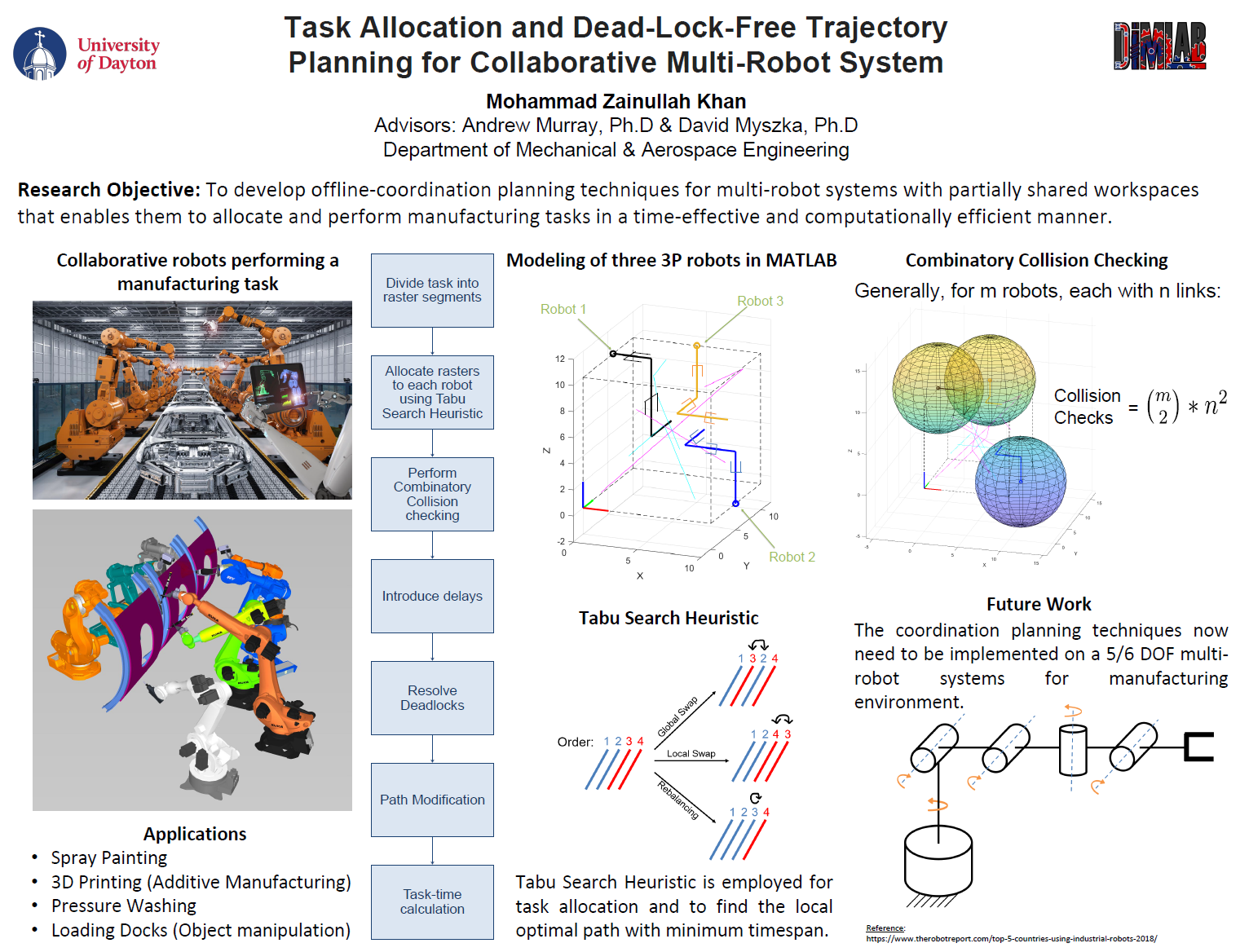
The above poster was made mid-way through the research and mentions the work on 5/6 DOF multi-robot systems as future work. This was performed during the second half of the research and a glimpse of it is provided below.
Single 5R Robot Performing the Rasters Alone (from two different views)
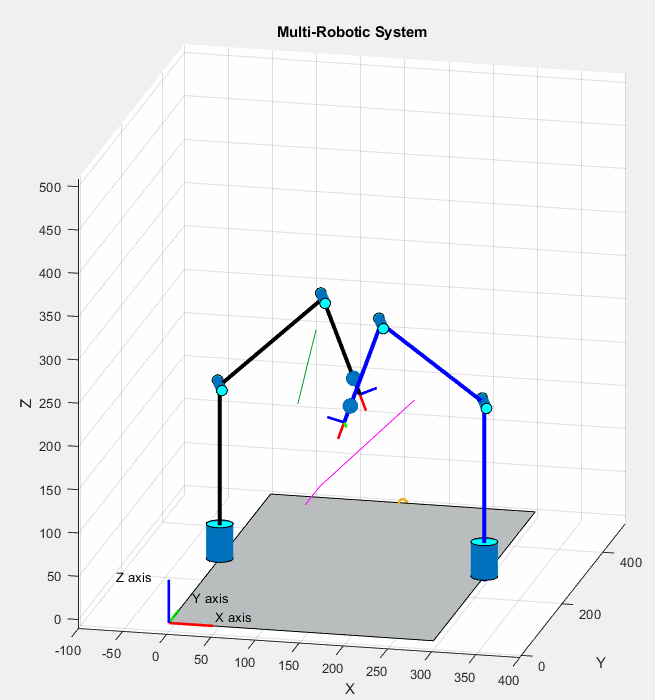
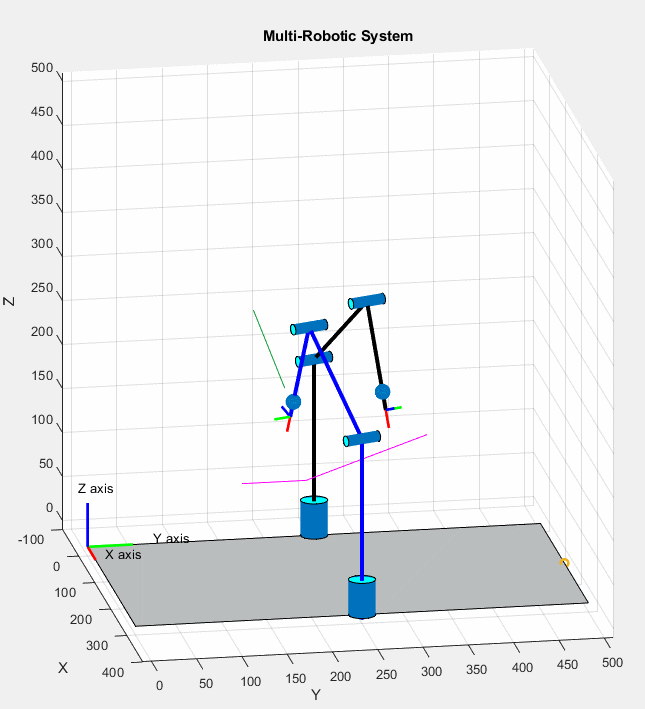
Two robots performing a task with collision detection activated
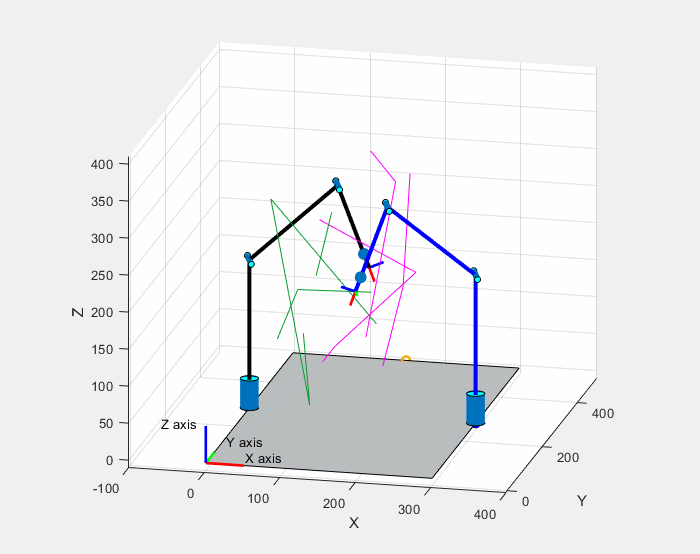
The collisions are being detected in this animation and the point of collision is shown as a red circle at the point of collision.
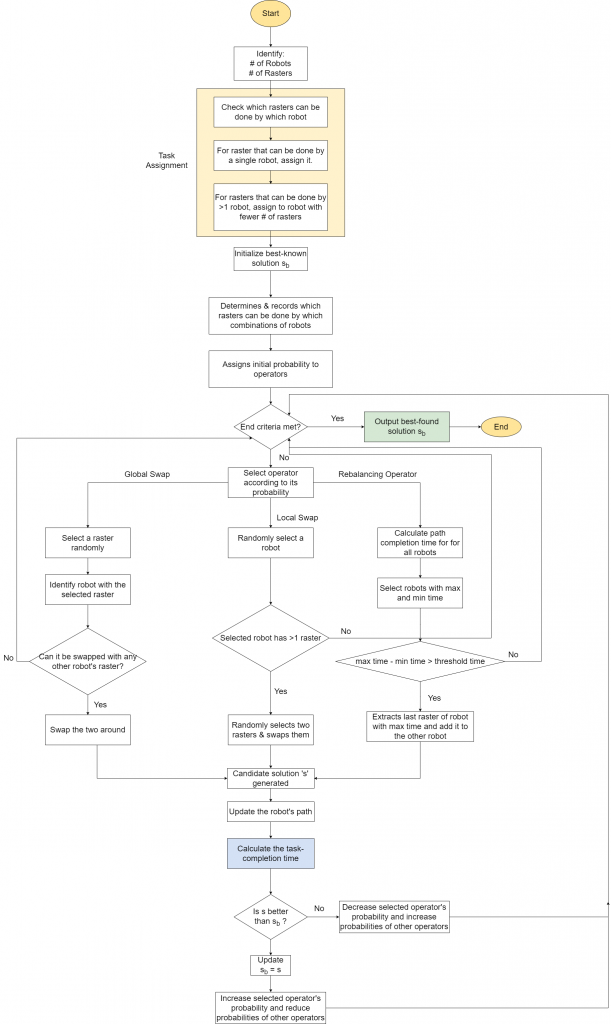
Video walking through the steps of the research
The path planning technique developed and simulated led to a massive 60% improvement in production efficiency for various industrial automation applications such as welding, painting, material handling, and manufacturing operations.
This was a rather quick overview of the research. I did not put in a lot of equations, methodology or anything to not make it look too complex. If you are interested in learning more about this research, you can view my full thesis here. Also, if interested, email me and I can share some cool animations that validate this methodology.
See my other projects below
Thank you for being here.
You can always reach out to me via email for any opportunities or just to say 'hi'. If you want to convince others that I will add great value to your organization, you can download and send my resume to them.